Concrete Mix Design as per IS 10262:2019 – Step-by-Step Guide with M25 Example
.avif)
Table of Content
Key Takeaways
- IS 10262:2019 is India’s official code for concrete mix proportioning, ensuring strength, durability, and cost-efficiency.
- Design Mix (used for >M20 grades) saves up to 15% cement over Nominal Mix methods.
- The guide walks through M25 mix design step-by-step—from water-cement ratio to aggregate adjustments.
- Learn to factor in seasonal moisture, workability, and exposure conditions using real project examples.
- BuiltX applies these IS standards to NGO and healthcare projects across India—ensuring your concrete is both structurally sound and cost-effective.
A poorly designed concrete mix design can lead to cracking, low strength, or excess cement usage — costing lakhs in repairs. That’s why IS 10262:2019 serves as India’s official guideline for calculating the right proportions of cement, aggregates, water, and admixtures to meet both performance and durability requirements.
This standard outlines two primary methods of mix proportioning:
- Design Mix Concrete – Used for grades above M20, where proportions are calculated based on performance targets (like strength, workability, and exposure conditions).
- Nominal Mix Concrete – Used for grades up to M20, with predefined mix ratios. Though simpler, it often leads to excess cement usage and must be approved by the engineer-in-charge (IS 456:2000, Clause 9.3).
In fact, studies show that switching from nominal to design mix can reduce cement consumption by 10–15% in large-scale projects (Source: CPWD Concrete Guidelines 2021), making it more cost-effective and sustainable.
This blog walks you through a step-by-step mix design process as per IS 10262:2019, with a detailed M25 concrete example, including adjustments for water content, aggregate moisture, and field conditions.
Can a building change lives? Discover how construction drives real social impact.
Step 1: Gather All Required Data for Concrete Mix Design
To design a concrete mix for a specific grade, the following information is essential:
- Grade Designation: Specifies the target strength of the concrete.
- Cement Type and Grade: Type and grade of cement to be used (if applicable).
- Maximum Nominal Size of Aggregate: Determines the largest aggregate size.
- Minimum Cement Content and Maximum Water-Cement Ratio: As specified, or based on exposure conditions.
- Workability: Desired workability at the time of placement.
- Method of Placing: Influences mix design (e.g., pumpable or manual placement).
- Degree of Site Control: Good or fair, or the established standard deviation value.
- Aggregate Types:
- Type of coarse aggregate.
- Type of fine aggregate.
- Maximum Cement Content: Upper limit for cement usage.
- Chemical Admixtures: Whether used, type, and extent of use.
- Mineral Admixtures: Whether used, type, and extent of use.
- Additional Requirements: Specific needs, such as early-age strength.
Step 2: Calculate Target Mean Strength of Concrete
Select the required concrete grade, classified as
- Ordinary Concrete: M10, M15, M20
- Standard Concrete: M25, M30, M35, M40, M45, M50, M55
- High Strength Concrete: M60, M65, M70, M75, M80
In the mix designation, 'M' refers to the mix, and the number indicates the characteristic compressive strength of a 150 mm cube at 28 days (N/mm²). For example, this M25 mix proportion gives a compressive strength of 25 N/mm².
Planning to build a hospital? Don’t miss this breakdown of licensing costs in India.
Table 1: Assumed Standard Deviation (Reference Clause 4.2.1.3, IS 10262: 2019)
Note:
- If test results are unavailable, standard deviation values from Table 1 can be assumed for initial design, which corresponds to good site control (proper cement storage, weight batching, controlled water addition, regular checks on materials, aggregate grading, moisture content, workability, and strength).
- For fair site control (deviations from good control), increase standard deviation by 1 N/mm².
Step 3: Choose the Correct Water-Cement Ratio in Concrete Mix Design
Determine the w/c ratio based on the 28-day compressive strength, using curves:
- Curve 1: Compressive strength of cement used from 33 to <43 N/mm²
- Curve 2: Compressive strength of cement used from 43 to <53 N/mm²
- Curve 3: Compressive strength of cement used ≥53 N/mm²
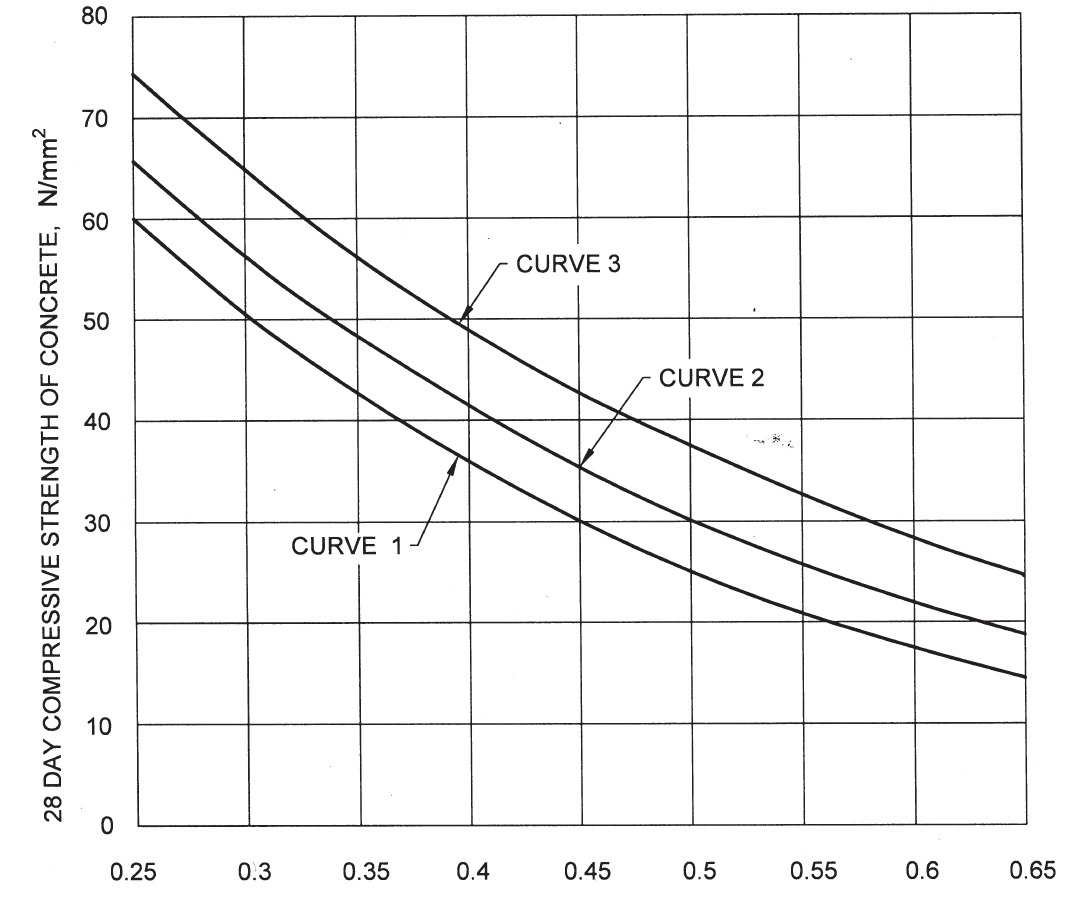
Note:
- Check the selected w/c ratio against the maximum w/c ratio for durability and adopt the lower value.
Table 2: Requirements of Durability (Reference Section 8.2, IS 456: 2000)
Step 4: Estimate Entrapped Air Content Based on Aggregate Size
Approximate entrapped air content in normal concrete is given by below table.
Table 3: Appropriate air content (Reference Clause 5.2, IS 10262: 2019)
For 20 mm nominal maximum aggregate size: 1% of concrete volume.
Step 5: Select Water Content and Make Water Adjustments
Determine water content per m³ of concrete from below table.
Table 4: Water content (Reference Clause 5.3, IS 10262: 2019)
Note:
- The water content in the above table is for SSD aggregates, angular coarse aggregates, and having 50 mm slump.
Example:
For 20 mm aggregate: Water content = 186 kg/m³.
Water Corrections:
1. Based on type of aggregate:
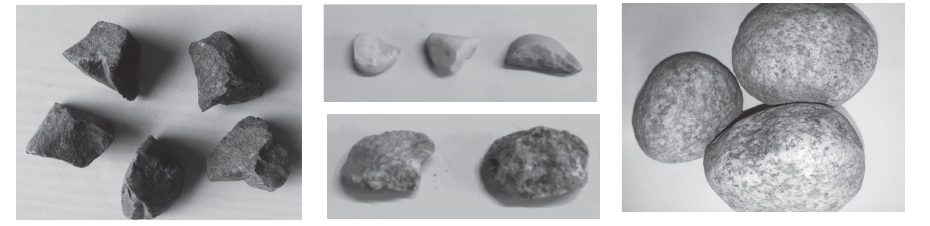
Table 5: Water correction for aggregate type based on shape
2. Based on slump value:
Table 6: Water correction for slump value
3. Based on chemical admixtures:
Table 7: Water correction for use of admixture
Step 6: Calculation of Cement Content
Calculate cement content using the w/c ratio and water content:
Mass of cement = Water content / w/c
Note:
- Check against minimum cement content for durability (Table 2) and adopt the higher value.
Step 7: Determine Volume of Coarse Aggregate from Grading Zone and Size
Determine the volume ratio of coarse aggregate to total aggregate from below table.
Table 8: Volume of coarse aggregate per unit volume of total aggregate (Reference Clause 5.5, IS 10262: 2019)
Note:
- These ratios are applicable for w/c = 0.5
- For pumpable concrete: Reduce ratio by up to 10%
Corrections:
Table 9: Correlation of w/c and change in ratio of volume of coarse aggregate to total volume of aggregate
Step 8: Calculate Quantities of Fine and Coarse Aggregates
Calculate aggregate volumes by subtracting the volumes of cement, water, and entrapped air from the total concrete volume (1 m³). Distribute the remaining volume based on the coarse aggregate ratio.
How safe is your construction site? Trace the evolution of worker safety rules and gear.
Step 9: Adjust for Aggregate Absorption and Moisture (Seasonal Correction)
Adjust water content based on aggregate absorption capacity and moisture content.
Step 10: Conduct Trial Mixes and Optimize the Design
Verify the mix proportions through trial batches:
- Measure workability of Trial Mix No. 1.
- Prepare two additional trial mixes (No. 2 and 3) with the same water content as Trial Mix No. 1 but vary the w/c ratio by ±10% while maintaining workability requirements.
Getting your concrete mix proportions right isn’t just about passing a lab test—it’s about ensuring long-term strength, workability, and cost-efficiency on site. With the IS 10262:2019 mix design method, you can confidently calculate everything from the target compressive strength to the exact quantities of cement, water, and aggregates—while meeting durability requirements laid out in IS 456:2000.
Whether you’re preparing an M25 concrete mix, adjusting for seasonal moisture, or planning a trial batch, this step-by-step guide ensures your design is both technically sound and field-ready.
At BuiltX, we help project teams across Delhi NCR, Bihar, Jharkhand, and West Bengal apply these IS standards to design mix India-wide for NGO and healthcare projects. Our engineers work closely with NGO construction partners, hospitals, and contractors to ensure every batch meets structural and sustainability benchmarks.
Have a BOQ or site condition that needs validation? We’ll review your mix design, water-cement ratio, and durability grade—for free. Book a 20-minute call with our engineer